THE CONSTRUCTION
Most aspects of building a musical instrument have remained the same since the 1600s. As if opening a window into the past, building a new instrument is an engaging and rewarding experience for both the violin maker and the musician.
Collaboration and dialogue are very important when choosing the elements that will determine the appearance and character of the new instrument, such as the model or the wood to be used.
In this way, it is possible for the customer to express his or her tastes and needs and to follow the development of the work on the instrument at every stage.
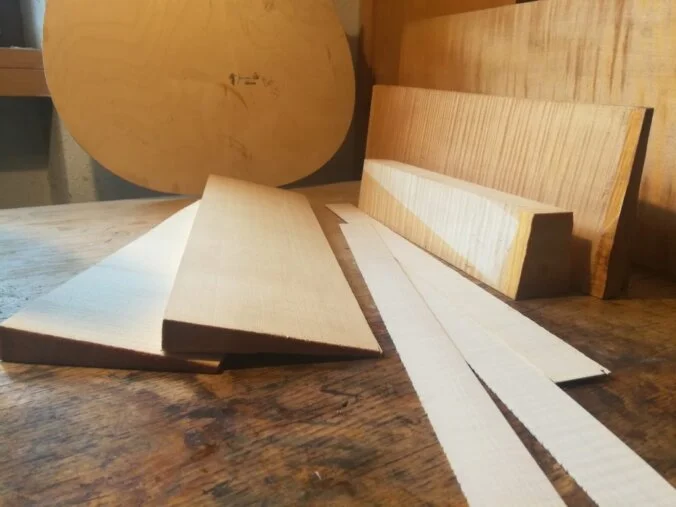
THE MATERIAL - THE BASE
The materials used in violin making have remained identical to those used in workshops 400 years ago.
The wood, thanks to its characteristics, contributes to the uniqueness of each instrument, precisely because an attempt is made each time to understand and use the potential of each piece to the full.
For the rest of the case harmony, the valuable and resistant Balkan maple is used.
Its marbling, sometimes very pronounced, is part of the instrument's beauty.
But the quality of the wood is not everything, it must be cut correctly, stored and prepared with proper seasoning.
Resonance spruce, picea excelsa, is used for the harmony board, which constitutes the ‘living’ part of the instrument, its voice.
THE PROCESSING
It is then up to the luthier to transform the pieces of wood into a unique and unrepeatable musical instrument.
Many of the tools and gestures performed in our workshop are practically the same as in the workshops of classical violin makers.
It takes patience and precision to go through all the different processes: the soundboard and back are hollowed out and given the right thickness, the ribs are bent, the curl is carved, and finally the difficult phase of preparing and applying the varnish is tackled.
Details make perfection, but perfection is not a detail.
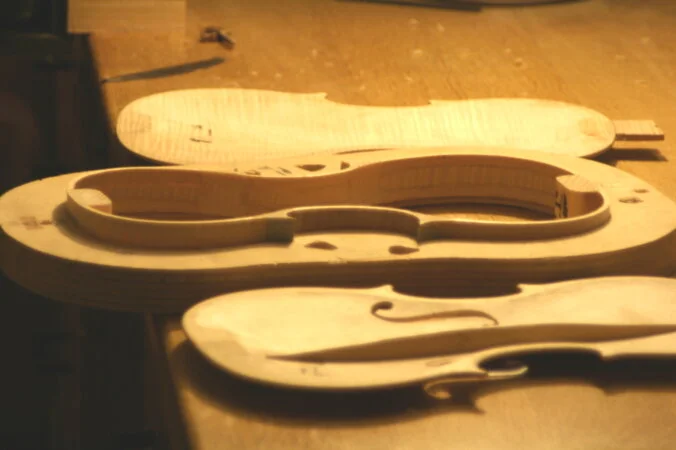
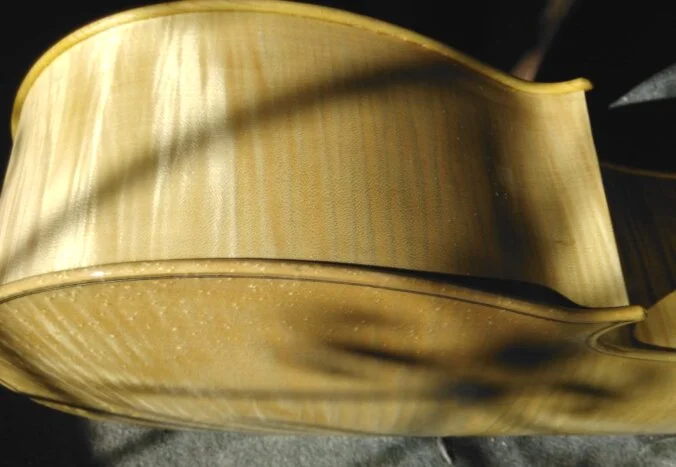
VARNISHING
The varnish must beautify and protect the instrument without altering its acoustic qualities.
In our atelier, we use a classic oil varnish prepared especially for us.
We start by applying preparatory coats, then move on to the actual varnish.
Finally, we finish the instrument with a coat of shellac.
For antique instruments (only at the specific request of the customer) we use systems developed over time, observing and gaining experience in restoration.
THE CERTIFICATE
A unique certificate of authenticity is supplied with each instrument, attesting to its quality and originality by means, above all, of photographs of the finished instrument.
Also included with the certificate is an enclosed CD with photographs of each stage of manufacture, from the raw material to the finished, varnished instrument.
This undoubtedly guarantees that the instrument is of high craftsmanship and is in no way made with semi-finished products or the like, and is built and cared for in every part by Maestro Cortesi.
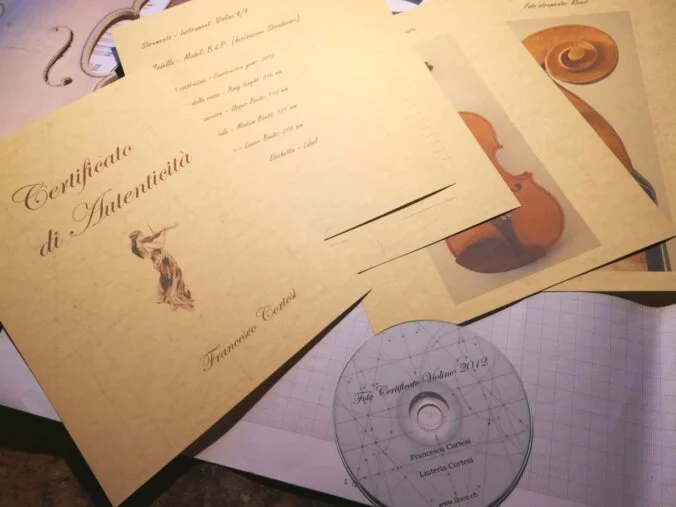